Crushing equipment is classified into jaw crusher, gyratory crusher cone crusher, roller crusher circular disc crusher, impact crusher, and hammer crusher depending on the design and the working principle.
Jaw crusher: This crusher comes with many advantages like a high crushing ratio, consistent quality product as well as a simple design and reliable operation. It also offers easy maintenance and low operating costs. Materials that do not exceed 320MPa.
Similar to the previous stage, each crushing stage will be expected produce an exact output for the next stage. Aggregate producers that pair the right crusher liners to the correct stage will be the most efficient and, consequently, the most profitable.
Cone crushers have large crushing ratios, high efficiency, and uniform particle dimensions. They are utilized mainly to crush fine and medium-hardness rocks.
Impact crushers: They can crush materials up to 100-500mm in length. Its compressive strength could be as high as 350MPa. It is distinguished by its large crushing ratio, cubic particles after crushing and a uniform particle size. It is widely used in the highway engineering industry to crush stones. middle.
Hammer crushers are is suitable for crushing the minerals of various brittle materials. The compressive strength of the material must not exceed 100MPa and the humidity should not exceed 15%.
Consider these factors when selecting a crusher
When choosing a crusher the type, the hardness, particle size of material coming in and going out along with the construction site and output of the crushed material should be considered in full.
1. The material's hardness
Different materials have different degrees of hardness. In general, the greater the hardness, the higher the crushing difficulty coefficient. When crushing medium or hard stones, jaw crushers is recommended as the primary crusher. If you are crushing soft or medium-hard stones, cone, counterattack or hammer crushers can be utilized directly.
2. Specifications for materials
Jaw crushers can be utilized to crush large amounts of material. However when the stone is small and requires a specific gradation or gradation, a combination crusher and screening equipment, like a jaw crushing, is necessary. Combination crushing equipment consists of a cone crusher or an impact crusher and the hammer crusher.
3. The material's humidity
The amount of water present in the material will also affect the choice of mill liners foundry. If the water content is too large, the fine-grained material will become agglomerated or adhere to the coarse-grained material due to the rise in humidity, thereby increasing the viscosity, reducing the discharge speed, and making the Productivity has fallen. It can even cause obstruction to the discharge port and cause production to stop in some instances.
4. The degree of cleavage formation of the ore
The amount of cleavage formation of the ore directly affects the productivity of the crusher. It is very easy to break the ore along the cleavage edges after it has been crushed. The crusher's efficiency is greater when an ore that has an extremely dense structure. .
5. Particle size both inbound and outgoing
The incoming and outgoing particle size is used to judge the type and crushing level of the equipment needed for crushing. If the quantity of coarse particles in the crushed material is greater than the discharge port's capacity or the ratio of the largest block of ore to the feed port is high then crusher liners, the crushing ratio, must be reached (the particle size prior to crushing, and the size the size after crushing). This can reduce productivity.
If the amount of small particles (close to or smaller than the dimensions of the discharge port) of crushed material is large or the ratio of the biggest chunk of crushed ore in relation to the width of the port for feeding is low The crushing ratio that can be achieved is small, so the productivity is also increased. Secondary crushing, or multi-stage crushing, could be necessary if the feed particle size and the discharge particle size are huge.
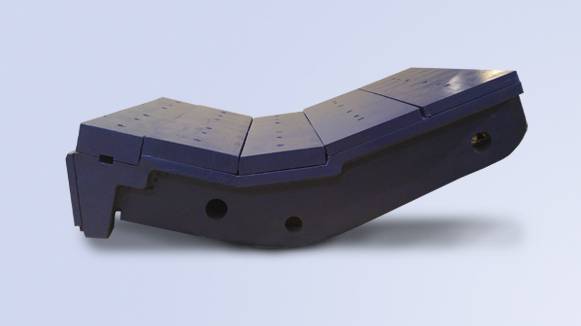
6. Requirements for Yield
To determine the size of crushing equipment it is essential to know what the output requirements are. The higher the output requirement is, the bigger the capacity of the crushing equipment required and the input and output will increase.
7. Construction site
The particular situation of the construction site is the primary factor affecting the selection of crushers, such as the size of the site for construction, the exact place of the crusher equipment, etc.
Comments
Post a Comment